Od kilku lat jest niezwykle modna. Pokryte nią dachy wyglądają elegancko i szlachetnie. Jednak także jej dotyczą ograniczenia wynikające z uwarunkowań lokalnych i specyfiki budynku.
Pokrycia z blachy płaskiej są dostępne w formie wstępnie profilowanych arkuszy albo blachy nawiniętej na kręgi z przeznaczeniem do łączenia na rąbek. W zależności od konstrukcji dachu może to być rąbek kątowy, stojący pojedynczy lub stojący podwójny – tak zwany felc.
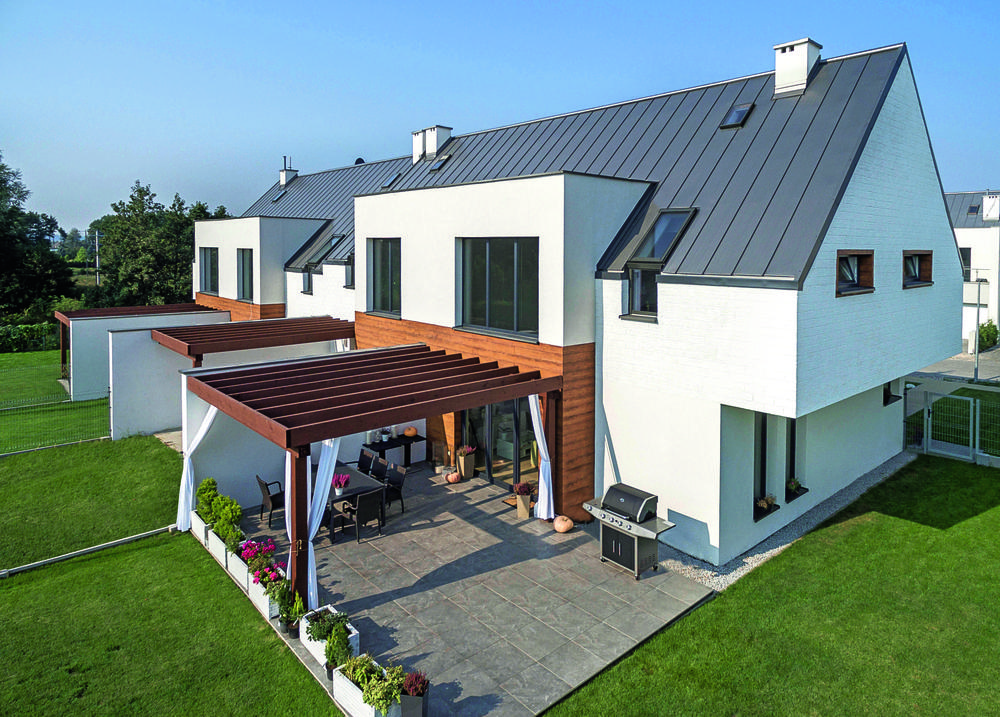
Panele do łączenia na rąbek są fabrycznie przygotowane pod długość połaci, mają też fabrycznie przygotowane otwory montażowe, co ułatwia montaż i skraca czas układania pokrycia
Fot. BLACHY PRUSZYŃSKIBlachy do wyboru
Stalowa powlekana. Występuje w formie arkuszy lub paneli zatrzaskowych o grubości rdzenia 0,5, 0,6 lub 0,7 mm. Waży około 5 kg/m2. Niektóre arkusze mają jedno lub dwa przetłoczenia usztywniające. Rdzeń blachy musi być zabezpieczony przed korozją, dlatego jest ogniowo powlekany cynkiem, stopem cynku z aluminium albo magnezem, który jest bardziej odporny na środowisko agresywne i wilgoć. Na stopie alucynku dodatkowo umieszcza się warstwę powłoki polimerowej, która chroni również brzegi stali w kręgach.
Najczęściej jednak blachy są dodatkowo pokryte powłoką organiczną stanowiącą warstwę dekoracyjną i zewnętrzne zabezpieczenie przed wpływem czynników atmosferycznych. Nanosi się ją na metalizowany rdzeń po uprzednim zabezpieczeniu go z obu stron farbą gruntującą i antykorozyjną. W zależności od rodzaju materiału, z jakiego są wykonane, mają różną grubość i trwałość.
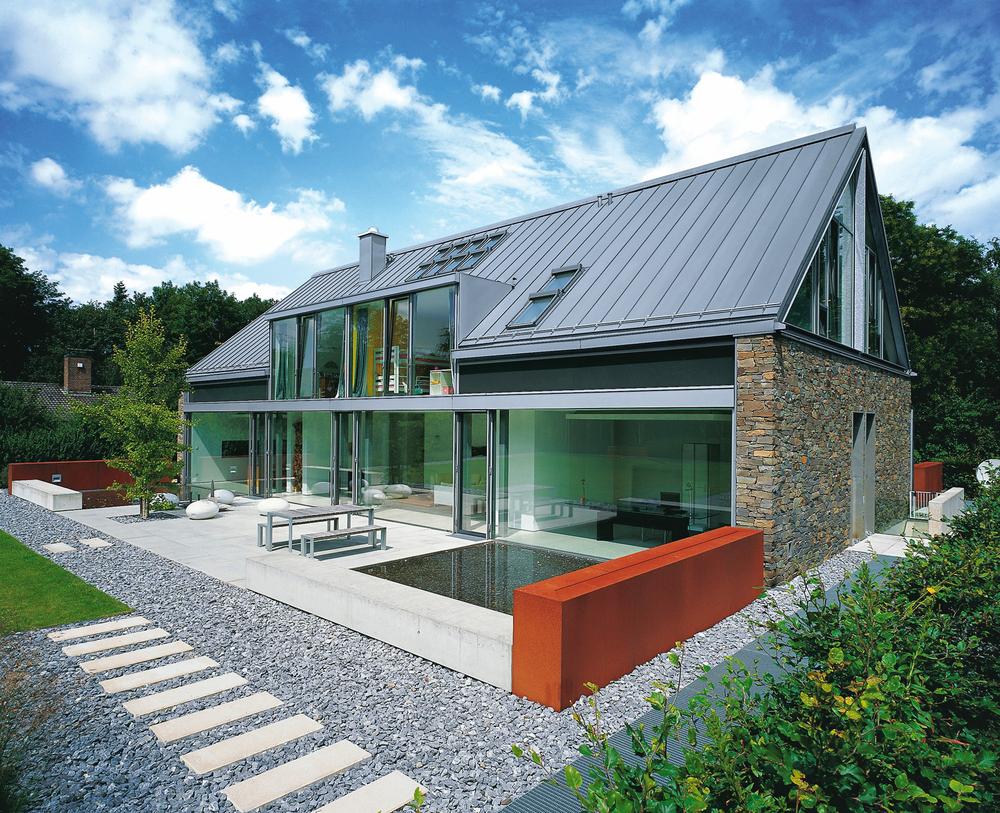
Cynkowo-tytanowa. Jest dostępna w formie nawiniętych na kręgi pasów oraz arkuszy łączonych na rąbek stojący pojedynczy i podwójny, rąbek kątowy oraz paneli zatrzaskowych. Grubość rdzenia to 0,7 mm. Stop cynkowo-tytanowy nie wymaga powłok zabezpieczających, bo naturalnie patynuje. Jest to jednak proces długotrwały, a świeża gołowalcowana blacha jest narażona na trudne do usunięcia zabrudzenia, dlatego większość pokryć patynuje się wstępnie już podczas procesu produkcji.
Blacha cynkowo-tytanowa nie może pracować w agresywnym dla siebie środowisku. Najgroźniejsza jest niezgodność fizykochemiczna z innymi metalami, a niedopuszczalny kontakt z surową miedzią, niezabezpieczoną stalą i żelazem. Nie powinna też stykać się bezpośrednio z kwaśnym drewnem (pH niższe od 4,5). Ponieważ szkodliwe są także środki przeciwgrzybiczne, ogniochronne i przeciw owadom drewnożernym używane do ochrony drewna, nie powinno się układać jej bezpośrednio na płytach wiórowych i ze sklejki. Nie wolno również dopuszczać do kontaktu blachy ze świeżym betonem i gipsem, przy czym podłoże gipsowe jest dla stopu tak agresywne, że nie wolno na nim kłaść blachy nawet na warstwie maty separacyjnej. Bezpieczne dla tego stopu metale to ołów, cynk, stal nierdzewna, tytan, cynowana miedź i aluminium.
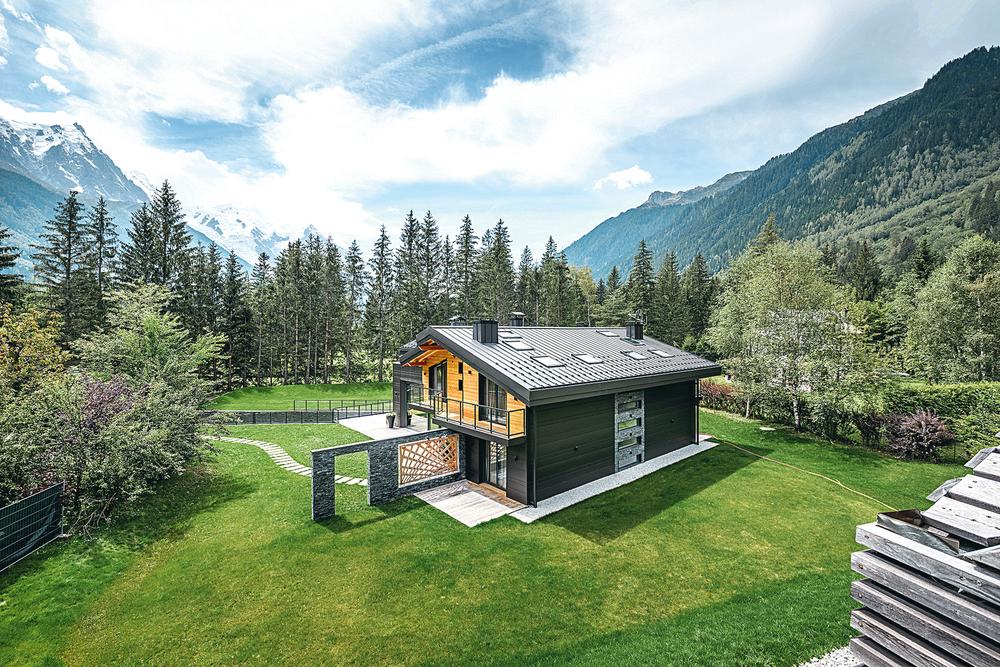
Blacha aluminiowa lub będąca stopem aluminium i cynku jest dostępna w formie paneli łączonych na rąbek stojący zatrzaskowy o grubości rdzenia 0,8 mm. Można też kupić ją w formie pasów do samodzielnego formowania rąbków i do obróbek. Waży około 2,5 kg/m2. Powierzchnia arkuszy może być pokryta poliestrową powłoką organiczną albo warstwą alucynku. Na te ostatnie jest często naniesiony transparentny lakier przedłużający żywotność stopu i eksponujący metaliczny wygląd.
Blacha ze stali nierdzewnej także jest dostępna w formie pasów (o powierzchni matowej, bardzo albo lekko błyszczącej bądź o niewielkiej chropowatości) do samodzielnego wyprofilowania rąbków. Przed korozją chroni ją wytwarzana trwale na powierzchni i samoistnie odnawiana pasywna warstwa tlenku chromu.
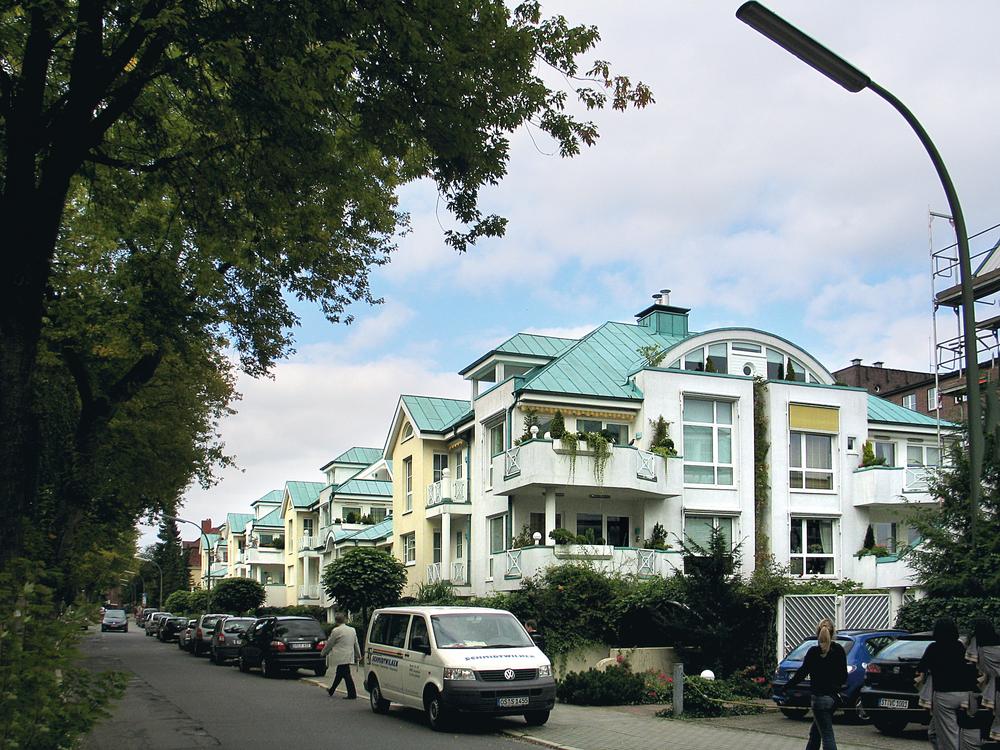
Blachę miedzianą kupuje się wyłącznie w postaci nawiniętych na rolki pasów grubości 0,6 mm do samodzielnej obróbki i wyginania rąbków stojących. Dzięki temu, że w kontakcie z powietrzem samoistnie pokrywa się ochronną warstwą patyny, nie wymaga żadnych zabiegów konserwacyjnych. Nie może się stykać z metalami, które mają wyższy od niej potencjał elektrochemiczny (cynkiem i jego stopami, stalą ocynkowaną, aluminium, a także elementami miedziowanymi galwanicznie). Bezpieczne są dla niej łączniki i akcesoria ze stali nierdzewnej i cynowanej, z ołowiu i cyny.
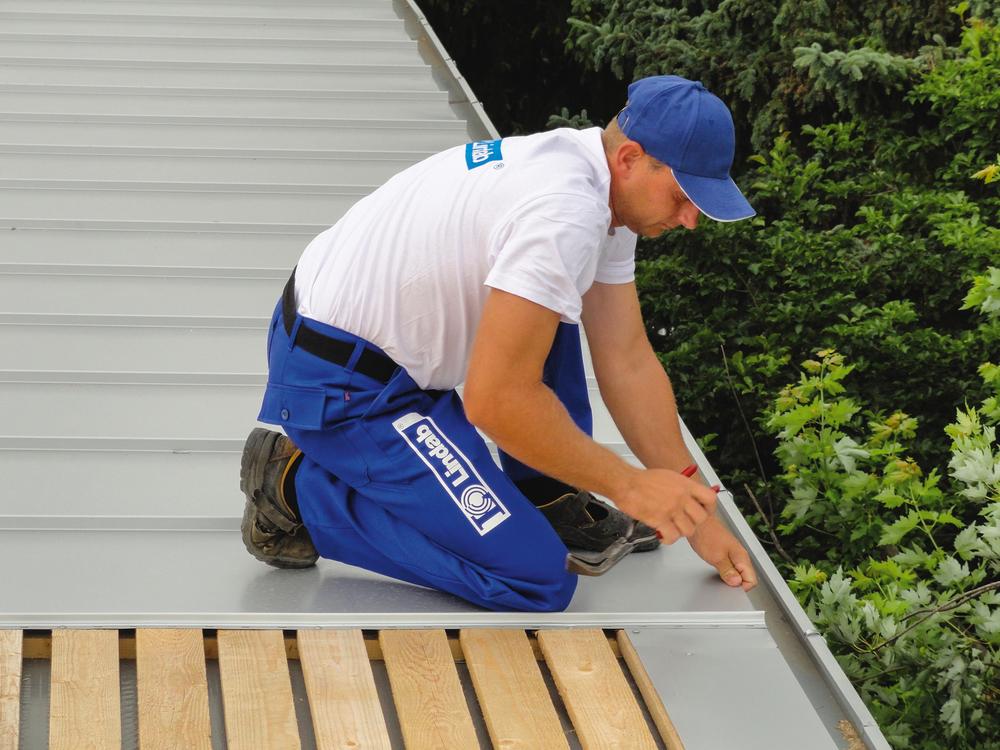
Na jakie dachy
Najbardziej uniwersalna ze względu na szczelność jest blacha płaska do łączenia na felc, czyli podwójny rąbek stojący. Jej połączenia najpierw się zaciska, a potem dodatkowo zagina. Nadaje się na połacie o spadku od 1:10, czyli 5,7º, ale przy zachowaniu pewnych warunków (odwodnienie dachu za pomocą zewnętrznych rynien wiszących, układanie arkuszy pełnej długości bez połączeń wzdłużnych z dodatkowym uszczelnieniem połączeń poprzecznych) można kłaść ją na dachach o nachyleniu wynoszącym 1:16, czyli 3,6º.
Większość materiałów pokryciowych z blachy jest przeznaczona na połacie o nachyleniu 1:7, czyli od 8º.
Najbardziej stromych połaci wymaga blacha układana na rąbek kątowy – 1:1,4, czyli 35º. Specyficznym przypadkiem są krawędzie stropodachów, ścianki attykowe oraz szczyty łuków, na przykład wolich oczek – tam powierzchnie są niemal całkowicie poziome. Zabezpiecza się je standardowymi obróbkami blacharskimi, ale z dodatkowym uszczelnieniem. Z kolei jeśli dach ma zaprojektowane odwodnienie w postaci rynien leżących, to w zależności od systemu połać nie może mieć spadku mniejszego niż 18 º lub 30º.
Długość połaci może być dowolna, pod warunkiem że dach ma odpowiednie nachylenie i dopuszcza się stosowanie łączeń wzdłużnych. Blachą na podwójny rąbek stojący można bez łączeń wzdłużnych przekryć połać o długości do 10 m. Najdłuższe są arkusze blachy cynkowo-tytanowej – przy spełnieniu określonych warunków dotyczących szczelności i rozszerzalności mogą mieć nawet 16 m. Maksymalna długość połaci, którą można pokryć arkuszem blachy, ma ogromne znaczenie podczas jego ruchów termicznych. Im dłuższy arkusz, tym mocniej się rozszerza i kurczy, więc tym większy jest przyrost jego długości podczas upałów i zmniejszanie jej zimą. To grozi fałdowaniem blachy, a w skrajnych przypadkach nawet pękaniem łączeń – luz montażowy pozostawiany przy łącznikach jest bowiem przewidziany tylko do pewnego stopnia rozszerzalności. Zbyt mocno skurczony arkusz pociągnie łączniki albo zamki rąbka, rozszczelniając połączenie. Z kolei zbytnio wydłużony może zniszczyć obróbki okapowe, a blacha się pofałduje.
Producenci zawsze też podają minimalną długość połaci, zazwyczaj jest to 70 lub 80 cm. Teoretycznie od tej strony nie ma ścisłych ograniczeń, bo każdy materiał można przyciąć. Może to jednak mieć znaczenie praktyczne; na dachach łamanych, gdzie górna lub dolna strefa ma długość 70 cm, wybór blachy o minimalnej długości arkuszy 70 cm (zamiast 80 cm) oznacza brak konieczności cięcia każdego arkusza. To przyspiesza prace, a dodatkowo korzystnie wpływa na estetykę dachu i jego trwałość, bo przycięte krawędzie nigdy nie są idealnie równe.
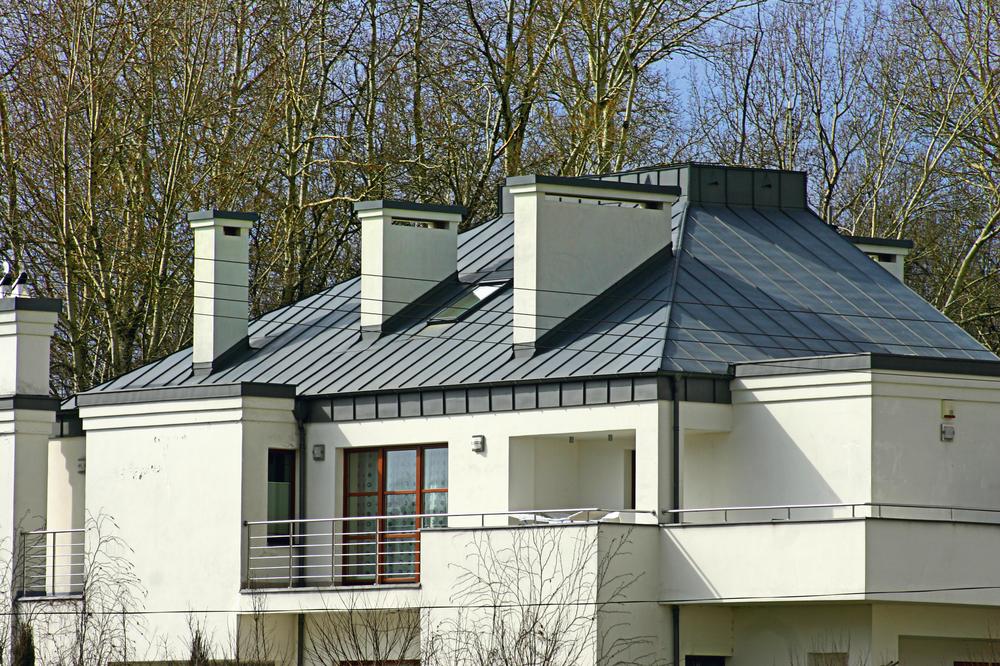
Usytuowanie budynku
Najgroźniejsze dla pokrycia są śnieg i porywisty wiatr. Śnieg zalegający na dachu dłużej niż trzy tygodnie, topniejący i zamarzający, przekształca się w lód. Zmieniają się wtedy jego gęstość i ciężar, co musi być uwzględnione w obliczeniach statycznych dachu. Wzrasta też ciśnienie hydrostatyczne wody, co zwiększa podciąganie kapilarne na łączeniach blachy i naraża je na przeciekanie. W wypadku takich dachów niezbędne są więc dodatkowe uszczelnienia rąbków. Z kolei na terenie wietrznym blaszane pokrycia mocno falują i głośno dudnią. Dlatego powinno się tam stosować panele z warstwą włókniny wygłuszającej albo pod każdym arkuszem układać wzdłużnie specjalną taśmę, na przykład z pianki polietylenowej. Poza tym wielkoformatowe arkusze są narażone na oderwanie przez wiatr. Groźne są zarówno gwałtowne podmuchy wciskające się w nieszczelności i prące na arkusz od spodu, jak i te wywołujące ssanie przy kalenicy i zewnętrznych krawędziach dachu. Najlepiej wybierać materiały układane na sztywnym poszyciu, bo deskowanie stanowi stabilny podkład i ogranicza ryzyko zerwania lekkich arkuszy przez silny podmuch, a przy tym razem z systemową warstwą separacyjną układaną pod blachą dobrze tłumi hałas podczas zawieruchy.
Koniecznie trzeba też uwzględnić ewentualny wpływ agresywnego środowiska. Kwaśne deszcze na terenach silnie uprzemysłowionych, ciągły kontakt ze słoną parą wodną nad morzem bądź stała obecność ptaków, których odchody są bardzo żrące, to czynniki istotne dla trwałości pokrycia. Najlepiej sprawdzą się wtedy blacha naturalna aluminiowa, miedziana, cynkowo-tytanowa albo ocynkowana. Blachy stalowe powlekane powłokami organicznymi mogą się łuszczyć, a odsłonięta blacha może zacząć korodować szybciej, niż przewiduje gwarancja.
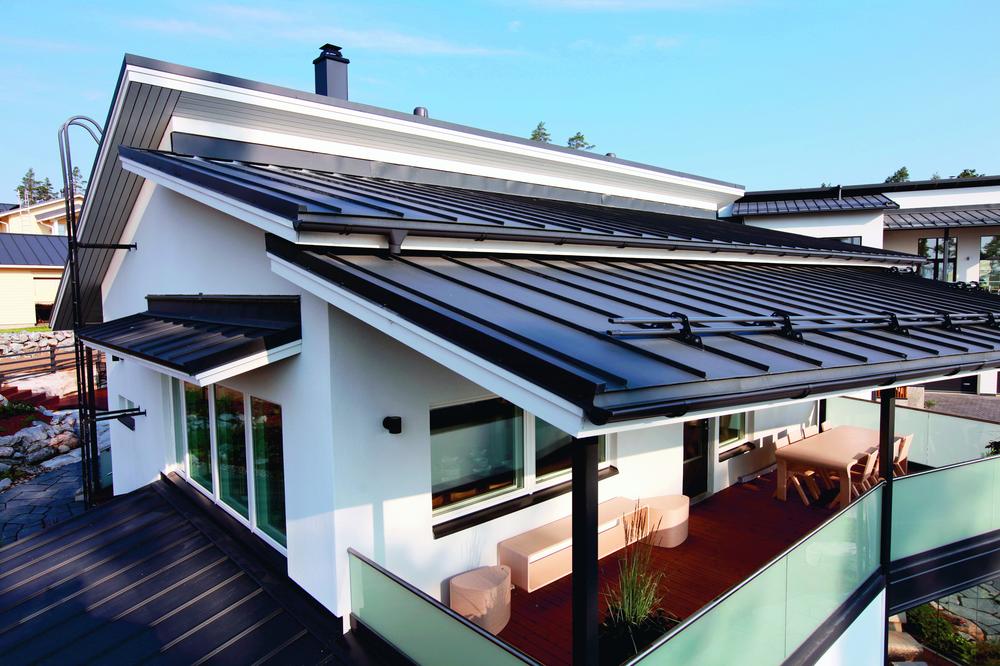
Panele na zatrzask
Panele z rąbkami stojącymi są znacznie prostsze w układaniu niż blacha i nie wymagają budowania na dachu sztywnego poszycia z desek. Wytwarza się je z blachy ocynkowanej powlekanej poliestrem, puralem lub innym rodzajem kolorowej powłoki ochronno-dekoracyjnej (zależnie od producenta) grubości 0,5 mm, a czasem też 0,6 lub 0,7 mm. Dostępne są także w droższej wersji – z blachy cynkowo-tytanowej. Mają szerokość od 27,5 do 54 cm, ich długość zaczyna się już od 50 cm, a górna granica sięga nawet 10 m, z tym że panele tak pokaźnych wymiarów przygotowywane są na zamówienie. Zazwyczaj stosuje się elementy o długości równej długości połaci dachu, czyli 3-7 m.
Panele mają już otwory montażowe i wzdłuż krawędzi fabrycznie wyprofilowane pionowe rąbki wysokości 25, 32 lub 37 mm, które są tak ukształtowane, że można łączyć sąsiednie elementy, zatrzaskując je. Połączenie takie jest proste, solidne i szczelne.
Niektóre panele mają wytłaczaną nieregularną fakturę, która nadaje im ciekawy wygląd i dodatkowo usztywnia materiał. Inne mają płytkie, podłużne przetłoczenia. Dostępne są również panele z włókniną poprawiającą ich izolacyjność akustyczną o blisko 6 dB na spodniej stronie.
Pokrycie z paneli waży 4,8-5 kg/m2. Nadaje się na dachy o kącie nachylenia połaci nie mniejszym niż 8o (14%).
Przed zamówieniem paneli trzeba zmierzyć długość połaci – na jej podstawie ustala się długość paneli – oraz długość okapu, czyli szerokość płaszczyzny dachu. Pozwoli to dobrać wymiar łat i ustalić liczbę paneli potrzebnych do pokrycia połaci.
Układanie. Gdy nie przewidujemy sztywnego poszycia, na krokwiach rozpościeramy wysokoparoprzepuszczalną membranę dachową. Jej pasy biegną od dołu, równolegle do okapu.
Najpierw nabija się kontrłaty grubości nie mniejszej niż 2,5 cm. Mocuje je wzdłuż grzbietów krokwi tak, żeby membrana znajdowała się między nimi a krokwiami. Prostopadle do kontrłat przybija się lub przykręca łaty. Ich rozstaw powinien wynosić 25-30 cm. Szerokość łat to 5 cm, a grubość dobiera się do rozstawu krokwi: rozstaw 60 cm – grubość łaty 3 cm; rozstaw 90 cm – grubość łaty 3,5 cm; rozstaw 120 cm – grubość łaty 4 cm. Możliwe jest również wzmocnienie więźby poszyciem z desek lub płyt zaizolowanym papą bądź membraną dachową. Paneli nie układa się jednak bezpośrednio na poszyciu jak zwykłą blachę płaską. Trzeba zbudować podkonstrukcję z kontrłat i łat.
Radosław Murat
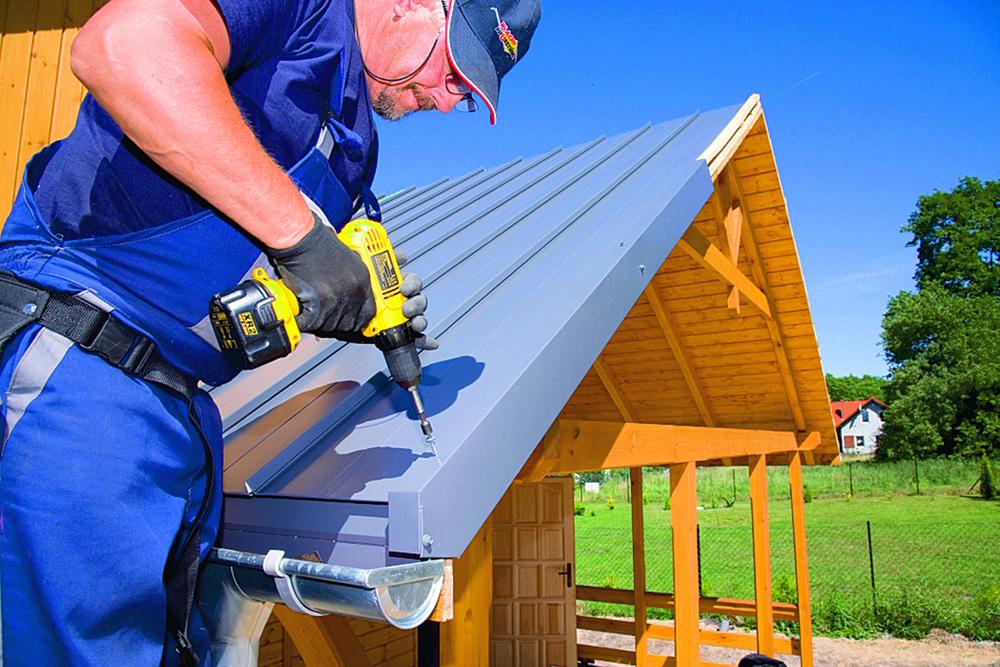
Dlaczego nie powinno się kłaść papy pod blachę płaską?
Tradycyjna blacha płaska (nie mówimy o panelach do łączenia na rąbek) przeznaczona jest do układania na sztywnym poszyciu, które nieco się różni od tego, które izoluje się papą bądź wykańcza gontami bitumicznymi. Powstaje najczęściej z desek układanych ażurowo, czyli z około 1-1,5 cm odstępami, które trzeba też zachować między płytami drewnopochodnymi, jeśli użyje się ich zamiast desek. Wszystko po to, aby zapewnić wentylację spodniej strony pokrycia. Dlatego też nie jest tu wskazana izolacja z papy, która by taką wentylację uniemożliwiła. Dopuszczalne, a nawet wskazane jest układanie pod blachą mat separacyjnych (strukturalnych), które mają z wierzchu warstwę sztywnych, splątanych włókien sztucznych (stąd popularna wśród dekarzy nazwa makaron) zapewniających przepływ powietrza pod blachą. Dzięki temu nie gromadzi się tam wilgoć, nie tworzą się skropliny i blacha jest trochę chłodzona. Mata separacyjna jest też potrzebna, jeśli poszycie powstało z desek impregnowanych, ponieważ impregnat jest „agresywną” substancją, mogącą mieć niekorzystny wpływ na blachę. Jeśli poszycie powstaje z płyt drewnopodobnych, trzeba użyć mat strukturalnych połączonych z membraną wysokoparoprzepuszczalną. Ponieważ płyty w ograniczonym stopniu pozwalają wentylować spód pokrycia, powstające tu skropliny spłyną po membranie do rynien.
Radosław Murat
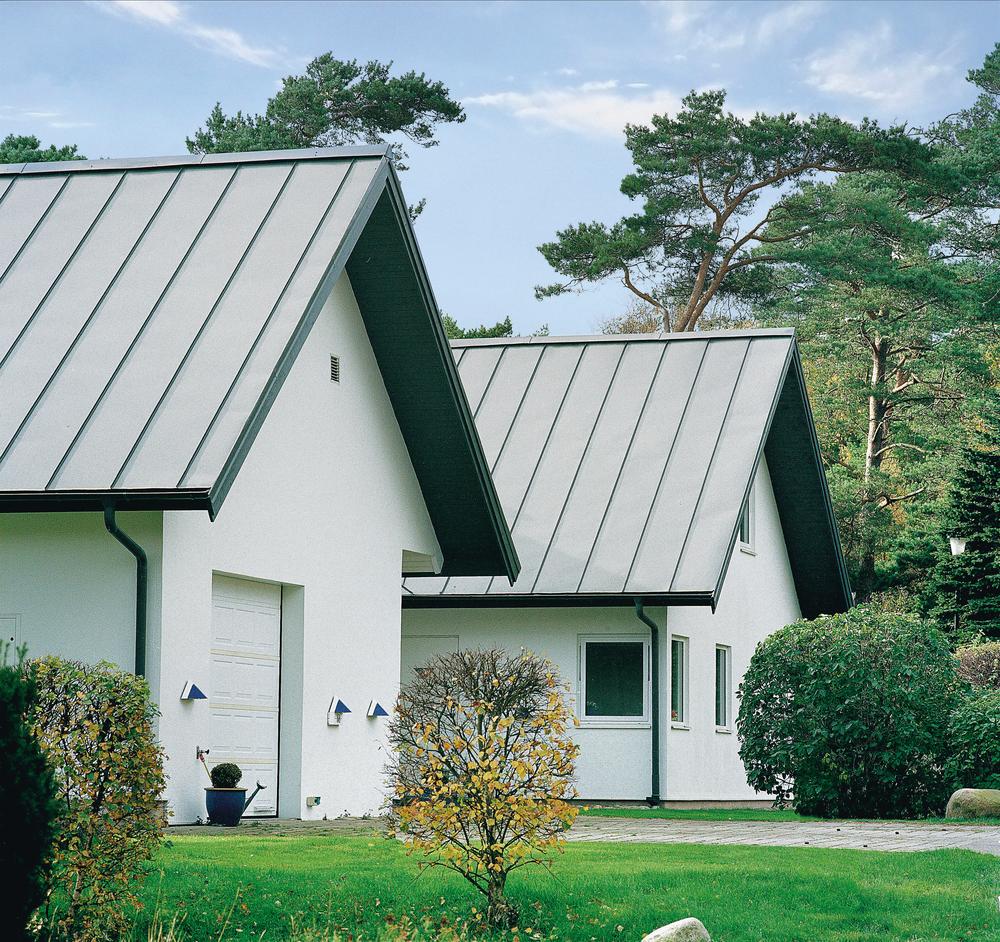