Niby-deski
Elewacyjna alternatywa
Deski kompozytowe, w których drewno jest tylko jednym ze składników, są alternatywą zarówno dla tradycyjnej oblicówki drewnianej, jak i okładzin z PCW. Jakie są ich rodzaje i jak się je montuje?
Kompozytami nazywamy materiały składające się z kilku rodzajów surowców trwale ze sobą połączonych. Ich proporcje dobiera się tak, aby jak najlepiej wykorzystać ich zalety w danym materiale. W okładzinach tego typu jednym ze składników są włókna drewniane lub mączka drzewna łączone w zależności od rodzaju kompozytu z tworzywem sztucznym albo cementem. Ponieważ istotną część składu procentowego takich paneli stanowi materiał naturalny, są one ciekawą alternatywą dla tych, którzy nie chcą stosować na elewacji całkowicie sztucznego sidingu z PCW. Ich wygląd, struktura oraz cechy fizyczne będące rezultatem dużej zawartości drewna zadowolą też zwolenników naturalnych materiałów. Panele z kompozytu skutecznie imitują prawdziwe deski, a pod niektórymi względami użytkowymi są nawet lepsze. Przede wszystkim nie trzeba ich co kilka lat konserwować. Są odporne na szkodniki i mniej wrażliwe na korozję biologiczną niż naturalne deski. Dzięki dodatkowi tworzywa sztucznego lub cementu nie wypaczają się ani nie skręcają tak jak drewno. Są też bardziej wytrzymałe i odporne na uderzenia. Nie pojawiają się na nich zadry, a ich powierzchnia jest zazwyczaj bardziej jednolita niż prawdziwych desek. Ta ostatnia cecha dla jednych jest zaletą, dla innych wadą.
Elementy kompozytowe docina się i obrabia, używając powszechnie dostępnych narzędzi do drewna. Najpopularniejsze niby-deski są zrobione z rozdrobnionego drewna połączonego z polimerami. Odrębną grupę stanowią wyroby włóknocementowe.
Kompozyty to materiały stosunkowo młode. Nie określają ich klasy jakościowe, jak to jest w przypadku drewna, stali i betonu. Najlepiej więc kupować panele elewacyjne od uznanych producentów. Mamy wówczas pewność, że ich jakość jest trwała.
Wytłaczane drewno z plastikiem
Ten rodzaj desek kompozytowych jest zbudowany z włókien drewnianych lub mączki celulozowej oraz polimerów termoplastycznych (polipropylen, polichlorek winylu, polietylen).
To najpopularniejsza okładzina kompozytowa. Zawartość drewna wynosi w niej 40-70%, pozostałą część stanowią tworzywa sztuczne. Materiały te po uplastycznieniu tworzywa sztucznego są mieszane z dodatkami, między innymi z pigmentami nadającymi im kolor, antyutleniaczami oraz uniepalniaczami. Z powstałej masy wytłacza się odpowiednie profile desek.
Czasami proces technologiczny przebiega inaczej i produkcja jest dwuetapowa. Najpierw wytwarza się granulowany kompozyt, z którego dopiero po jego ponownym uplastycznieniu formuje się końcowy produkt. Do wytwarzania desek z kompozytów drzewno-polimerowych (inaczej desek WPC) często wykorzystuje się granulaty tworzywa sztucznego pochodzące z recyklingu, drewno gorszej jakości z nasadzeń przemysłowych, a także odpady drewniane. Zużyte deski kompozytowe mogą być ponownie przerabiane na tworzywo o podobnych właściwościach. Jednak możliwości recyklingu kompozytów są bardziej ograniczone niż w przypadku materiałów jednorodnych.
Z kompozytu drzewno-polimerowego można formować na wytłaczarce różne kształty. Deski mogą być pełne, mieć profil jednościenny lub budowę komorową. Pełne produkuje się z dodatkiem środków spieniających, które obniżają ich wagę. Deski kompozytowe są bardziej elastyczne niż naturalne drewno, niektóre mogą być więc używane na ścianach łukowych (o dużym promieniu łuku). Profile komorowe oraz pełne są często dwustronne. Nadają się więc nie tylko na fasady, ale także na ogrodzenia i wolno stojące przesłony, które widać z obu stron.
Kompozyty drzewno-polimerowe są zazwyczaj barwione w masie. Dla uzyskania ciekawszej faktury ich powierzchnia może być szczotkowana lub lekko metaliczna, wyglądająca z daleka jak oksydowane aluminium.
Nasiąkają wodą w o wiele mniejszym stopniu niż prawdziwe drewno. Jednak dodatek celulozy powoduje, że w zacienionych miejscach mogą się na nich po pewnym czasie pojawić plamy pleśni. Ich konserwacja nie jest uciążliwa – polega na myciu wodą ze środkami czyszczącymi. Nie trzeba ich impregnować ani malować (zabezpiecza się tylko docięte miejsca). W razie zaplamienia lepiej je myć, niż szlifować, bo są pokryte środkiem hydrofobowym (zmniejszającym nasiąkliwość deski i ułatwiającym spływanie wody), a tarcie usuwa go z ich powierzchni.
Tworzywa sztuczne, które stanowią duży procent ich składu, są nieodporne na promienie UV, dlatego deski pod wpływem warunków atmosferycznych mogą zmieniać barwę. Aby temu zapobiec, w procesie produkcji miesza się je z dodatkami mającymi zmniejszyć ich wrażliwość na odbarwienie. Producenci często to sygnalizują i w materiałach informacyjnych prezentują oprócz koloru początkowego również barwę docelową, jaką po pewnym czasie (po roku lub dwóch) uzyska elewacja. Z niektórych desek kompozytowych trudno też usunąć zaplamienie. Uszkodzenia i zarysowania, jakie mogą się na nich pojawić podczas użytkowania, trudno jest naprawić. W wyniku działania mrozu może też zmniejszyć się ich wytrzymałość. Pod wpływem wysokiej temperatury deski kompozytowe zwiększają swoją objętość. Ich rozszerzalność zależy od temperatury i wilgoci. Wynosi ona 1-3 mm/m, dlatego podczas montażu należy zachować między elementami szczeliny dylatacyjne zalecane przez producentów.
Długość desek WPC wynosi od 3 do 6 m. Szerokość profilu to zazwyczaj około 20 cm, a grubość – kilkanaście milimetrów. 1 m2 desek kompozytowych na elewację wraz z akcesoriami do montażu kosztuje netto 200-220 zł.
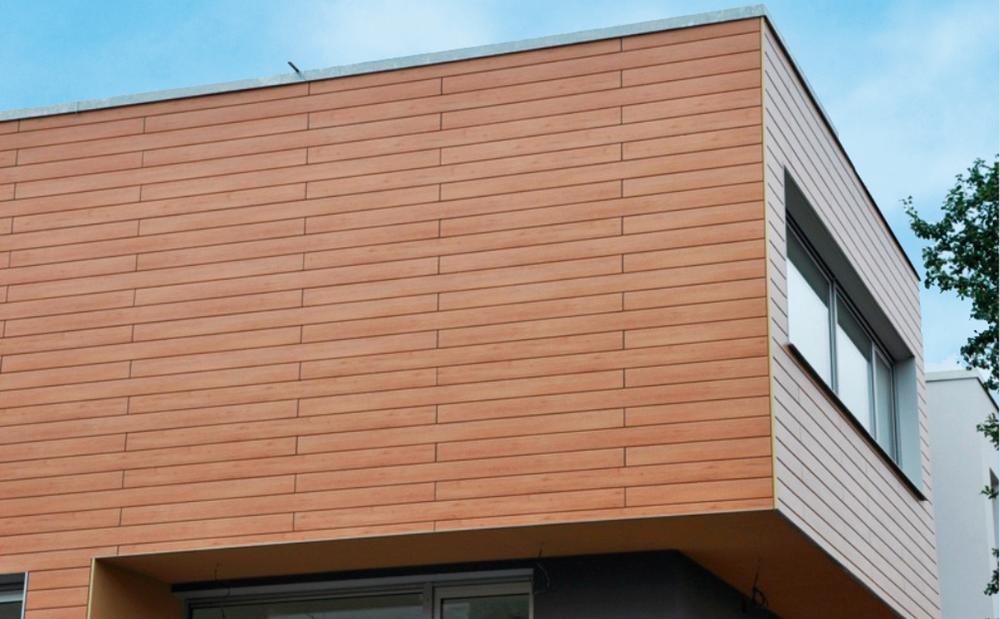
Niektóre rodzaje sztucznych desek do złudzenia przypominają drewno
fot. WERZALITW artykule znajdziesz:
- informacje o rodzajach desek kompozytowych
- analizę składu i budowy poszczególnych typów
- zalety oraz wady tego budulca
- zdjęcia i rysunki ułatwiające zrozumienie sposobu montażu
- adresy producentów i dysrybutorów tego typu materiału

Będziesz korzystać z całego miesiecznik.murator.pl, w tym archiwum, dodatków i wydań specjalnych